Laser cutting technology is rapidly evolving with exciting innovations. One key trend is the development of fiber and direct diode lasers, offering higher efficiency, better beam quality, and lower operating costs compared to traditional CO2 lasers. Additionally, advancements in automation and robotics are enabling more complex and intricate cutting patterns, improving productivity and precision. Software improvements, such as adaptive optics and real-time monitoring, are enhancing cut quality and reducing material waste. Furthermore, the integration of laser cutting with other technologies like additive manufacturing is opening up new possibilities for hybrid manufacturing processes. These trends are driving Laser Cutting Machines towards greater versatility, efficiency, and precision, expanding its applications across various industries.
Latest Advancements and Trends in Laser Cutting Technology

- • Faster Cutting Speeds: Advancements in laser cutting technology have led to increased cutting speeds, allowing for quicker production and turnaround times.
- • Enhanced Precision: Innovations in laser systems have improved cutting precision, resulting in cleaner cuts and finer details, even on intricate designs.
- • Versatile Material Compatibility: New developments have expanded the range of materials that can be effectively cut using laser technology, including metals, plastics, ceramics, and composites.
- • Automation Integration: Integration of automation features such as robotic arms and AI-driven systems has streamlined laser cutting processes, reducing manual labor and enhancing efficiency.
- • Improved Sustainability: Eco-friendly laser cutting technologies, such as fiber lasers with lower energy consumption and reduced waste generation, are becoming increasingly popular, promoting sustainability in manufacturing.
How Innovations Boost Speed, Accuracy, and Affordability.
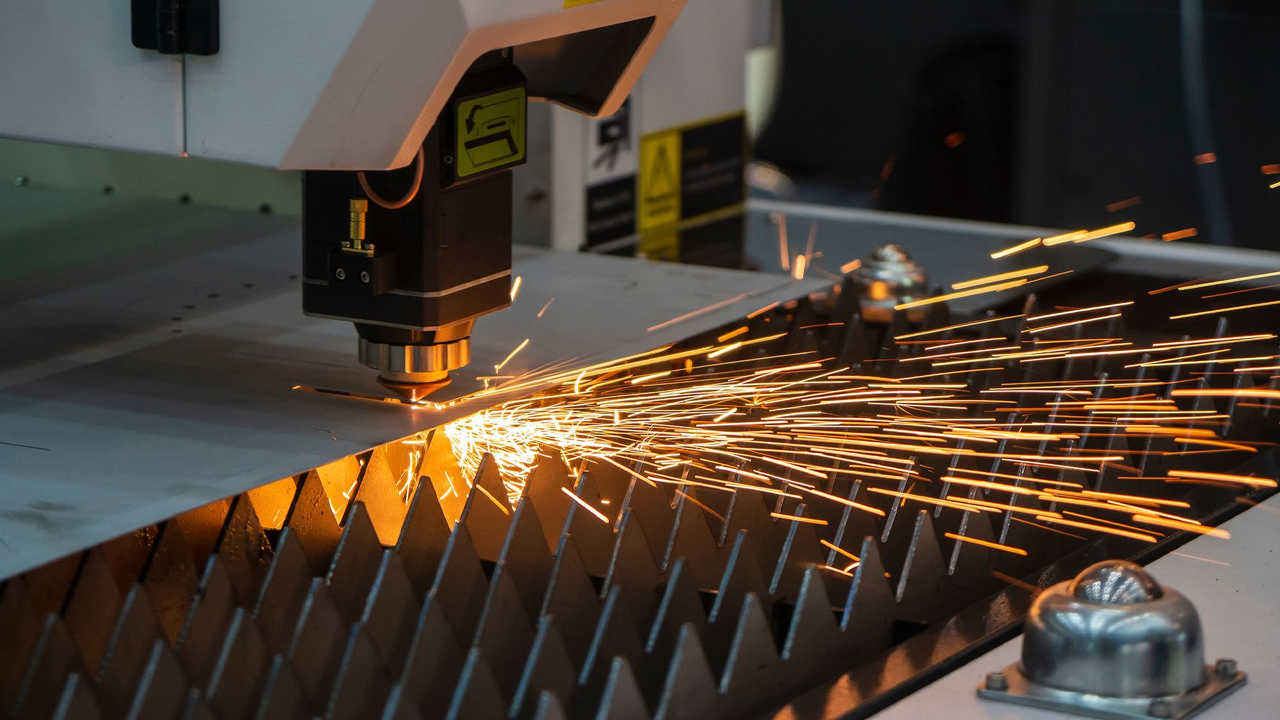
Efficiency:
- • Faster Processing Speeds: Innovations in laser sources and software algorithms enable faster cutting speeds, reducing processing times and increasing throughput.
- • Automation Integration: Integration of automation technologies streamlines workflow processes, minimizing manual intervention and maximizing production efficiency.
- • Real-Time Monitoring: Advanced monitoring systems provide real-time feedback on cutting performance, allowing operators to optimize parameters and minimize downtime.
Precision:
- • Enhanced Beam Quality: Improvements in laser sources and optics result in higher-quality beams, leading to cleaner cuts and finer detail reproduction.
- • Adaptive Optics: Adaptive optics systems dynamically adjust beam shape and focus, compensating for distortions and ensuring consistent cutting precision.
- • Path Optimization: Software algorithms optimize cutting paths to minimize material waste and improve accuracy, achieving precise cuts with minimal errors.
Cost-Effectiveness:
- • Reduced Material Waste: Path optimization algorithms and real-time monitoring systems minimize material waste, maximizing material utilization and reducing costs.
- • Lower Energy Consumption: Energy-efficient laser sources, such as fiber lasers, consume less power while maintaining high cutting speeds and precision, resulting in lower operating costs.
- • Increased Productivity: Faster processing speeds and automation integration lead to higher productivity levels, allowing for more parts to be produced in less time, ultimately driving down production costs per unit.
Examples of Cutting-Edge Applications
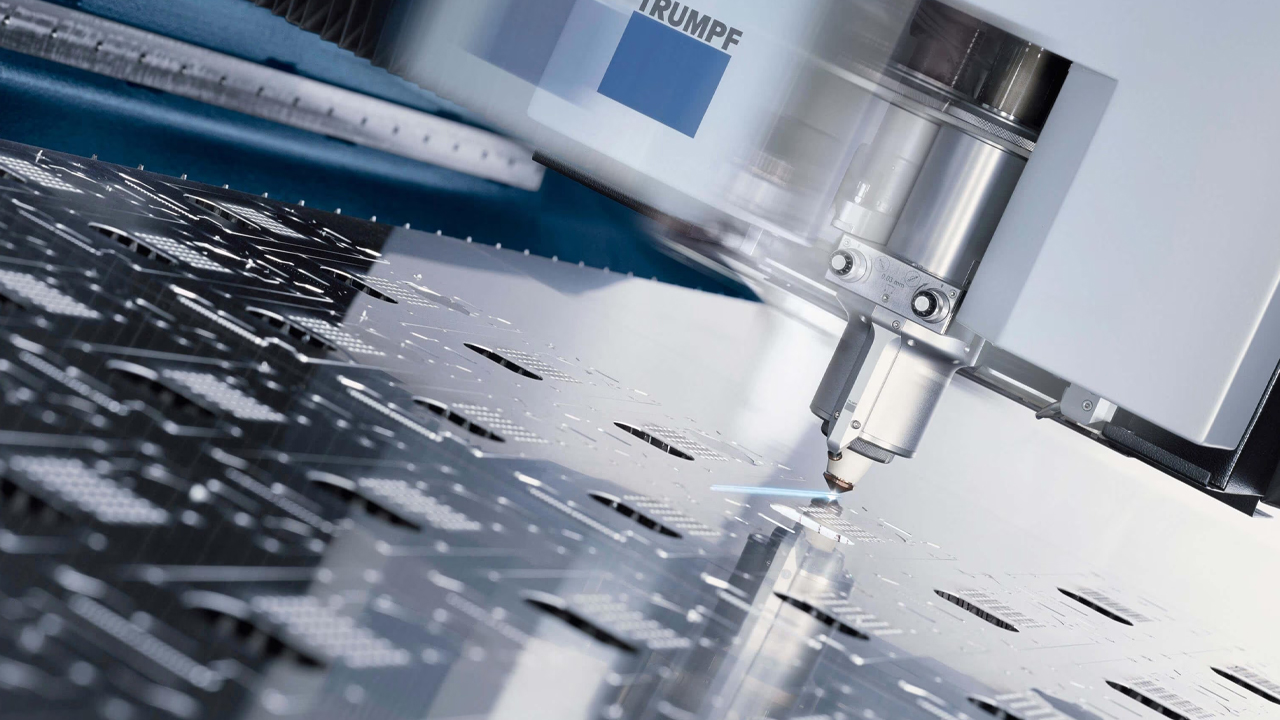
- • Automotive Industry: Precision cutting of intricate parts for engines and body components, enhancing performance and reducing weight.
- • Aerospace Sector: Manufacturing complex, lightweight structures for aircraft and spacecraft with high precision and minimal waste.
- • Medical Devices: Producing delicate and intricate medical implants and surgical instruments with exacting standards.
- • Electronics: Creating precise, small-scale components for smartphones, computers, and other electronic devices.
- • Jewelry Making: Crafting detailed and customized designs in metals and gemstones with high precision.
- • Fashion and Textiles: Cutting complex patterns in fabrics and leather for high-end fashion and accessories.
- • Architectural Models: Producing detailed models and components for buildings and structures.
- • Prototyping: Rapidly creating prototypes with precise specifications for testing and development in various industries.
Conclusion
In conclusion, the evolution of laser cutting technology, particularly the advancements in fiber and direct diode lasers, automation, and software, is revolutionizing manufacturing across industries. These innovations drive efficiency, precision, and affordability, enabling faster cutting speeds, enhanced precision, and reduced material waste. As laser cutting becomes more versatile and sustainable, its applications continue to expand, from automotive and aerospace to medical devices and electronics. By embracing these cutting-edge trends, businesses can stay ahead in the competitive landscape, delivering high-quality products with greater speed and accuracy while optimizing production costs.